Overview
Offshore wind is growing in popularity around the globe as more and more countries look to harness wind energy for electricity generation. The industry has continued to attract new markets and with more money than ever pouring into the market, OEMs have continued to advance their technologies. The rapid changes in the industry are a positive development but they also present new challenges. Developers and contractors must continually adapt to new market norms. In particular, WTG suppliers have increased the efficiency of their designs by increasing the overall size of the rotor blade, which in turn increases the turbine hub height. Larger turbines also require larger and heavier foundations. Advancements in WTG models have left contractors and vessel owners scrambling to retrofit their operating vessels and to build new next generation vessels with increased lifting capabilities.
This article provides an overview of our view on installation vessels currently available to serve the offshore wind turbine installation market and discusses the factors driving the demand for them to have increasingly greater crane capacity. This evaluation considers the announced wind turbine generator (WTG) models from the major suppliers and planned vessel upgrades and new build vessel information publicized by major installation contractors. Known alternative installation methods and installation of floating WTGs are also reviewed.
Beyond lifting capacity another challenge is that greater deck space will be required to ensure enough WTGs can be transported per cycle to maintain an economic transportation and installation cost. However, this metric is not addressed in detail in this article, as deck layouts are vessels specific, relating to OEM spacing requirements for their equipment and WTG assets.
Read more to find the answers to these questions:
- Why are turbines getting bigger?
- What does the future of WTGs look like?
- How will future WTGs be installed?
- How has the market reacted to next generation WTG models?
Why are turbines getting bigger?
Increasing the size of the WTG decreases the cost per unit of electricity generated for several reasons:
- Power output increases relative to the square of the swept radius of the turbine blades: a small increase in blade length leads to a large increase in power output.
- Longer blades require a higher hub height. Increasing the hub height provides access to faster and more consistent wind speeds away from the friction of the air-sea interface.
- In simple terms, one 10 MW turbine gives the same power output as two 5MW turbines. However, the levelized cost of energy is lower for the 10MW turbine since the associated infrastructure costs (steel, foundations, cables) and operational costs are lower for one turbine location compared to two. Across a 500MW wind farm it is very significant, from a financial perspective, if the number of turbines is reduced from 100 x 5MW to 50 x 10MW.
- Installation costs are lower when fewer WTG locations need to be visited.
- Onshore turbines are limited in size due to the need for onshore (road) transport and installation by onshore cranes. Offshore turbine components can be shipped directly to site and the available vessel-based cranes are much larger.
Figure 1 Height and Output Source: (1)
The size of offshore WTGs has increased rapidly over the past 5 years as the offshore wind industry has matured. However, these large jumps in size will become slower as the structural limits of current blade technology are reached.
Furthermore, as many of the best shallow water sites have already been built upon, new sites are being proposed further offshore and in deeper water. This requires longer jack up legs to achieve the required vessel height which limits the size of the WTG that can be installed.
What does the future of WTGs look like?
There are three major WTG suppliers that dominate the global offshore wind market (excluding the Chinese market) – these are Siemens Gamesa, Vestas and GE. The majority of currently operating offshore wind farms in Europe, and those under construction and development across Asia and USA, utilize one of these suppliers. Each of these suppliers has announced their next generation turbine model, specifications are summarised in Table 1.
Table 1 WTG Dimensions Source: (2) (3) (4)
Figure 2 shows a plot of rated power output against hub height using data from Table 1. Hub heights are site specific but have been estimated based on typical ranges. The linear nature of the relationship shows that for planned WTGs, required hook heights are in the order of 160m. It also suggests that hook heights can be expected to exceed 160m future, assuming WTG sizes continue to increase to 16MW and beyond.
Figure 2 Plot of hub height
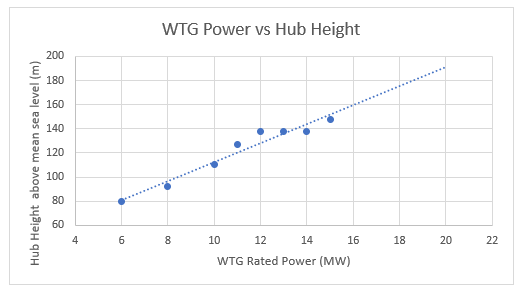
The existing fleet of WTG installation vessels used in the fixed offshore wind market in Europe are four or six leg jack up vessels, with a main crane lifting capacity of 1000-2000t, maximum lifting height of 60-100m and leg lengths of 50-100m. Some alterative 3-legged jack up vessel have been used in China, but these have not been considered due to the safety concerns they present.
Table 2 Example of Current WTG Installation Vessels source: (5) (6) (7) (8) (9) (10) (11)
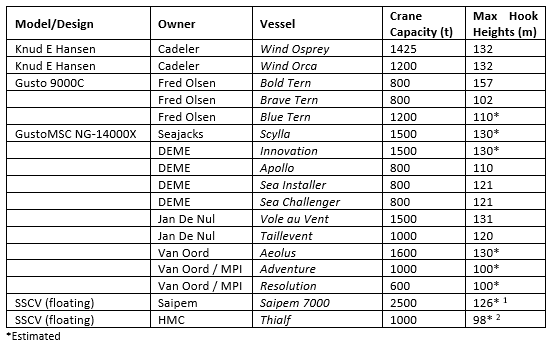
[1] Lifting operations draft at approximately 27.5m
[2] Lifting operations draft at approximately 26.0m
The vessel crane lifting height (dependent on leg length, crane capacity and required lifting radius) must be sufficient to install the tower and nacelle, which for future WTGs is likely to be in excess of 130m (as seen in Table 1). However, very few, if any of the current fleet vessels are capable of this (as shown Table 2). As projects move into deeper water with larger WTG models, the limits of the current vessel market will be quickly reached.
The major vessel operators are aware of these challenges and have addressed them in a number of ways, the following of which are considered in detail below:
1. Upgrading existing vessels with larger cranes;
2. Construction of new build vessels; and
3. Using alternative installation methods.
How has the market reacted to next generation WTG models?
Crane Upgrades for The Existing Fleet
Cadeler has announced crane upgrades for both the Osprey and Orca vessels in 2023/4. The main cranes on the upgraded vessels are planned to provide up to 1600t of lifting capacity with a 155 m hook height above deck.
Fred Olsen will upgrade the Bold Tern vessel with a 1600t crane in 2022 which is expected to have the highest crane in the market. With its upgraded crane and additional improvements to deck space and stability, Bold Tern will be capable of installing foundations up to 1500t and handling all known next generation turbines, including:
- SG 14-222DD
- MHI Vestas V164/174
- GE Haliade-X 12MW
Fred Olsen expects that up to five turbines can be carried onboard, depending on the WTG model.
Looking further ahead, some semi-submersible crane vessels – originally designed for lifting offshore oil and gas platforms – could be adapted to have a longer crane boom to meet the demands of the wind industry, however the economics of such an undertaking are in question due to the high capital cost of crane upgrades and high operating cost of this type of vessel.
New Build Vessels
Several major offshore contractors have released details of new build vessels. Lead time is 3-5 years, with most of these next generation vessels due for delivery in the mid-2020s. Quoted crane capacities are more than 2000t and maximum lifting heights are more than 160m.
Jan de Nul have announced the Voltaire vessel which is currently being built and is typical for the next generation class of vessels.
Figure 3 Indicative image of the planned Voltaire Jack-up Vessel Source: (7)
Wind Turbine Installation Vessel – Planned Upgrades and New Builds
Table 3 provides details of the vessel upgrades and new builds which have been announced by the major offshore installation contractors.
Table 3 Vessel upgrades and new builds (Source: (12), (13))
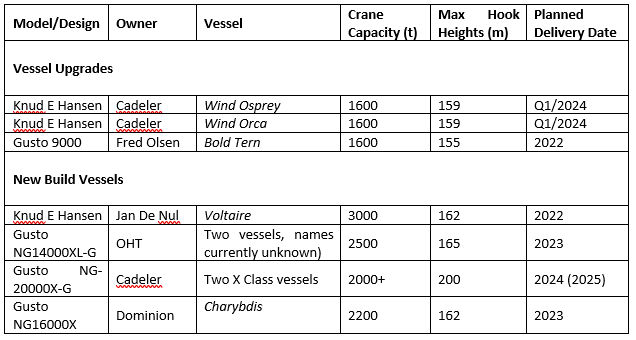
Floating Installation Methods
Heerema Marine Contractors will be executing a floating WTG installation of a fixed foundation solution at large scale for the Arcadis Ost project in 2022, using one of the four SSCVs in HMC’s fleet (14). Use of the SSCV removes the need to jack up from the seabed, removing the limitation of the length of the legs and eliminating risks posed by ground conditions.
Floating vessel installation of fixed foundations has the potential to allow a larger range of vessels to be used including those with a significantly higher hook height such as Sleipnir (hook height >140m) However, use of these floating vessels for WTG installation has thus far been commercially viable only where water depths or seabed conditions have been such that jack up vessels are not technically feasible. Additionally, the fleet of these vessels is quite small and capital costs most likely preclude building new craft specifically for WTG installation alone.
Figure 4 Heerema Sleipnir: (15)
Floating Offshore Wind Installation
The transport and installation methods for floating wind farms are in the early development stages, and much depends on the type of foundation and where it’s constructed. In some cases, it would likely be preferable to install the WTG onto the floating foundation using onshore cranes in the marshalling harbor and tow the complete structure to the site. However, this solution depends upon the floating foundation draft being shallow enough to make this feasible (e.g., typically less than 18m) in an existing port facility.
Where the foundation is in deeper water and offshore installation is required, the same constraints for fixed bottom wind turbines also exist for floating offshore turbine installation. Thus far only semi-Submersible Crane Vessels built for the oil and gas market have been used for the offshore installation of floating turbines (16). As WTGs grow, the lifting height will become the main constraint and even larger crane heights will be required.
As demand increases in the floating wind market, floating projects will also be competing with fixed bottom projects for installation vessel availability.
Figure 5 Chinas First Floating Wind Farm Source: (17)
With increased turbine size, only a small number of vessels have the required lifting height, and new or modified vessels will likely be required for 12MW+ turbines (18).
Conclusion
The dimensions of offshore wind turbines are still increasing and are likely to continue to do so. Additionally, projects will continue to move into deeper waters. For these reasons, required lifting heights and crane capacities are also projected to increase. Several major contractors and ship owners have already announced new build vessels, and more are expected to be announced, especially to service emerging markets in Asia and USA.
Floating WTG installation using semi-submersible crane vessels offers an alternative solution for locations with deeper water or difficult soil conditions. However, cranes on these much larger vessels will not easily be extended as lift height requirements continue to increase. Lifting in lower ballast states are possible but will adversely affect control and stability of the WTG during lifting compared to ballasted conditions.
OCA will continue to monitor this market and leverage our extensive experience in transport and installation for all types of offshore wind assets and infrastructure.
References
1. Bloomberg New Energy Finance. [Online] [Cited: July 22, 2021.] https://www.bloomberg.com/news/articles/2017-09-19/tipping-point-seen-for-clean-energy-as-monster-turbines-arrive.
2. GE. [Online] July 2021. [Cited: July 22, 2021.] https://www.ge.com/renewableenergy/wind-energy/offshore-wind/haliade-x-offshore-turbine.
3. Siemens Gamesa. [Online] July 2021. [Cited: July 22, 2021.] https://www.siemensgamesa.com/en-int/products-and-services/offshore.
4. Vestas. [Online] July 23, 2021. [Cited: July 22, 2021.] https://www.vestas.com/en/products/offshore-platforms#!grid_0_content_0_Container.
5. Cadeler. [Online] July 23, 2021. https://www.cadeler.com/en/vessels/.
6. DEME. [Online] July 23, 2021. https://www.deme-group.com/technology-0?f%5B0%5D=main_equipment%3A25.
7. Jan de Nul. [Online] 2021. [Cited: July 22, 2021.] https://www.jandenul.com/fleet/offshore-jack-installation-vessels.
8. Van Oord. [Online] 2021. [Cited: July 22, 2021.] https://www.vanoord.com/en/equipment/offshore-wind-installation-vessel/.
9. Seajacks. [Online] July 23, 2021. [Cited: July 23, 2021.] https://www.seajacks.com/wp-content/uploads/2018/01/Seajacks-SCYLLA-Specs-2018.pdf.
10. Fred Olsen Windcarrier. [Online] 2021. https://windcarrier.com/fleet/.
11. MPI Offshore. [Online] 2021. https://www.mpi-offshore.com/equipment.
12. Cadeler. [Online] June 2021. https://www.offshorewind.biz/2021/06/17/cadeler-to-upgrade-crane-gear-on-one-more-vessel/.
13. Fred Olsen Windcarrier. [Online] 2021. https://windcarrier.com/fleet/bold-tern/.
14. Buitendijk, Mariska. Heerema Develops Offshore Wind Construction Method Using Floating Vessel. s.l. : SWZ Maritime, 2019.
15. Jochem, Tacx. HMC Sleipnir. 2020.
16. Saipem. HYWIND. 2019.
17. Offshorewind.biz. [Online] 2021. [Cited: July 22, 2021.] https://www.offshorewind.biz/2021/07/13/chinas-first-floating-wind-turbine-heads-offshore/.
18. Carbon Trust. Phase II Summary Report – Floating Wind Joint Industry Project. 2020.
19. Heerema. [Online] 2021. [Cited: July 22, 2021.] https://hmc.heerema.com/news-media/news/parkwind-heerema-and-mhi-vestas-announce-a-revolutionary-construction-methodology-for-arcadis-ost-1.